Wat zijn de normen en tests voor de kwaliteitscontrole van LED neonverlichting en waarop zijn ze gebaseerd? Als koper moet je weten of de LED neon strip die je koopt getest is op veiligheid, energie-efficiëntie en milieubescherming. Omdat alleen fabrikanten die serieus aan deze tests voldoen, de betrouwbaarheid en kwaliteit van hun producten kunnen garanderen, zullen mensen zich vrij voelen om ze te kopen. Als je bijvoorbeeld de kleurtemperatuur en het lichtrendement van neonstripverlichting moet testen, moet je een integrerende bol of optisch testinstrument hebben. Als de fabrikant van LED neonstrips deze tests heeft uitgevoerd, zullen klanten zich meer op hun gemak voelen bij hun aankoop en zich geen zorgen hoeven te maken over mogelijke elektrische ongelukken of andere veiligheidsrisico's met het product.
De belangrijkste kwaliteitscontrolestandaarden voor LED neon strips zijn veiligheid, EMC, energie-efficiëntie en milieubescherming. Het testgedeelte omvat een elektrische veiligheidstest, een EMC-test, een fotobiologische veiligheidstest en een betrouwbaarheidstest voor het milieu. Daarnaast zijn materiaalkwaliteit, waterdichtheid (IP) en certificeringen zoals CE en RoHS ook belangrijke punten. Laten we het eens hebben over de normen voor kwaliteitscontrole van LED neon strips.
Wat are Te Main Qualiteit Control Standaarden voor LED Neon Sreizen?
Normen voor elektrische veiligheid
EN 60598-serie: EN IEC 60598 is een Europese regionale norm voor verlichtingsapparatuur die van toepassing is op alle soorten verlichtingsapparatuur, inclusief maar niet beperkt tot binnenverlichting, buitenverlichting, LED-lampen en lantaarns. Deze norm is afgeleid van de International Electrotechnical Commission (IEC) 60598 normenreeks, die wereldwijd breed toepasbaar is. De EN IEC 60598-norm wordt voornamelijk gebruikt om de prestaties van verlichtingsapparatuur te beoordelen op het gebied van elektrische veiligheid, mechanische veiligheid, thermische effecten en andere aspecten die betrokken kunnen zijn bij het installatie- en gebruiksproces om ervoor te zorgen dat het product voldoet aan de basiseisen voor veiligheid, gezondheid en milieubescherming. Een daarvan, EN 60598-2-14, is specifiek voor neonlampen en -lantaarns, inclusief constructief ontwerp, isolatieprestaties en spanningsweerstandstests.
IEC/EN 61347-2-11: Standaardiseert de veiligheidseisen voor voedingsapparatuur voor neonstrips. De Internationale Elektrotechnische Commissie (IEC) heeft de nieuwste versie van de veiligheidsnorm voor lichtbronbesturingen uitgegeven: IEC 61347-2-11:2024 "Veiligheid van besturingsapparatuur voor elektrische lichtbronnen - Deel 2-11: Bijzondere eisen voor diverse elektronische circuits voor gebruik met armaturen".
UL-normen: UL 8750 (Veiligheid van LED-apparaten) en UL 2108 (Laagspanningsverlichtingssystemen) voor de Noord-Amerikaanse markt. UL 8750 en UL 2108, als twee belangrijke UL veiligheidsnormen, reguleren de veiligheid van LED apparaten en laagspanningsverlichtingssystemen respectievelijk, en de recente herzieningen van UL 8750 hebben betrekking op de verfijning van de compatibiliteit van LED controllers en arrays (bijvoorbeeld, het aanvullen van de definitie van LED arrays voor speciale doeleinden), en de verfijning van de compatibiliteit van LED controllers en arrays. Recente herzieningen van UL 8750 omvatten compatibiliteits verfijningen voor LED controllers en arrays (bijv. het toevoegen van definities voor LED arrays voor speciale doeleinden), terwijl het testprogramma van UL 2108 zich meer richt op stabiliteitscontrole op systeemniveau.
Elektromagnetische compatibiliteit (EMC)
EMC verwijst naar de elektronische producten in het elektromagnetische veld interferentie grootte (EMI) en anti-interferentie vermogen (EMS) van de uitgebreide evaluatie, is een van de belangrijkste indicatoren van de kwaliteit van het product, elektromagnetische compatibiliteit door de test site en testapparatuur.
EMI-testen omvatten de volgende onderdelen:
- Geleide emissie (CE): Meting van elektromagnetische interferentie die wordt gegenereerd via geleidingspaden zoals elektriciteitsleidingen.
- Uitgestraalde emissie (RE): Meting van de intensiteit van elektromagnetische straling die wordt uitgezonden door apparatuur in verschillende frequentiebanden om ervoor te zorgen dat wordt voldaan aan gespecificeerde limieten.
- Harmonisch: Beoordeelt de harmonische impact van het apparaat op het elektriciteitsnet.
- Flikker: Evalueert de flikkereffecten van het apparaat op het elektriciteitsnet.
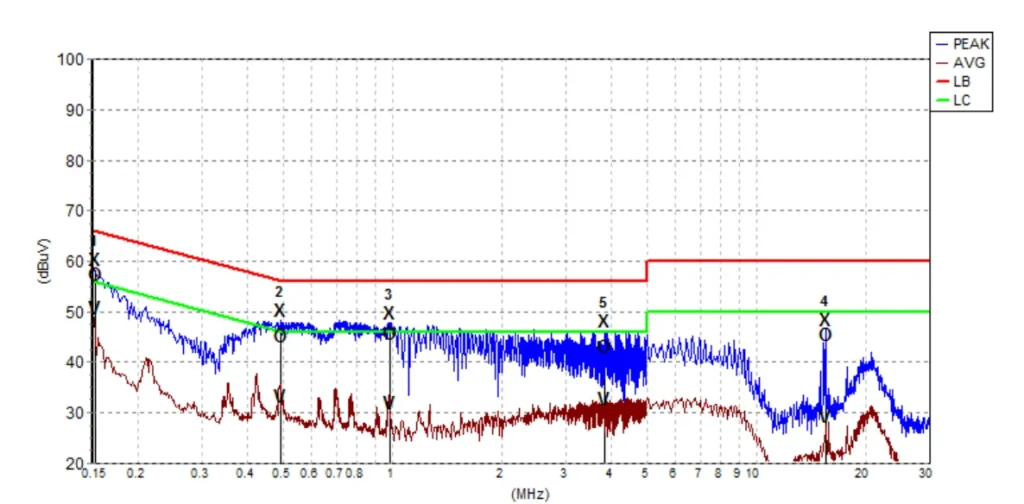
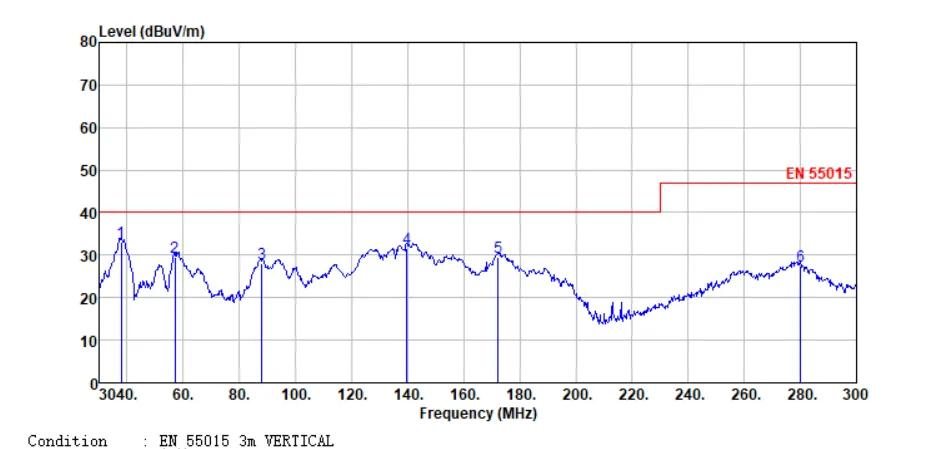
De EMS-test omvat de volgende onderdelen:
- Elektrostatische ontlading (ESD): Evalueert de immuniteit van de apparatuur voor elektrostatische ontlading.
- EFT: Simuleert de effecten van hoogfrequente elektromagnetische pulsen op apparatuur.
- Spanningsdaling (DIP): Evalueert de ongevoeligheid van een apparaat voor spanningsdalingen.
- Geleidende schommeling (CS): Evalueert het vermogen van een apparaat om geleide interferentie te weerstaan.
- Overspanning: Evalueert de immuniteit van een apparaat voor piekspanningen.
- PSMS: Evalueert de immuniteit van een apparaat voor industriële magnetische velden.
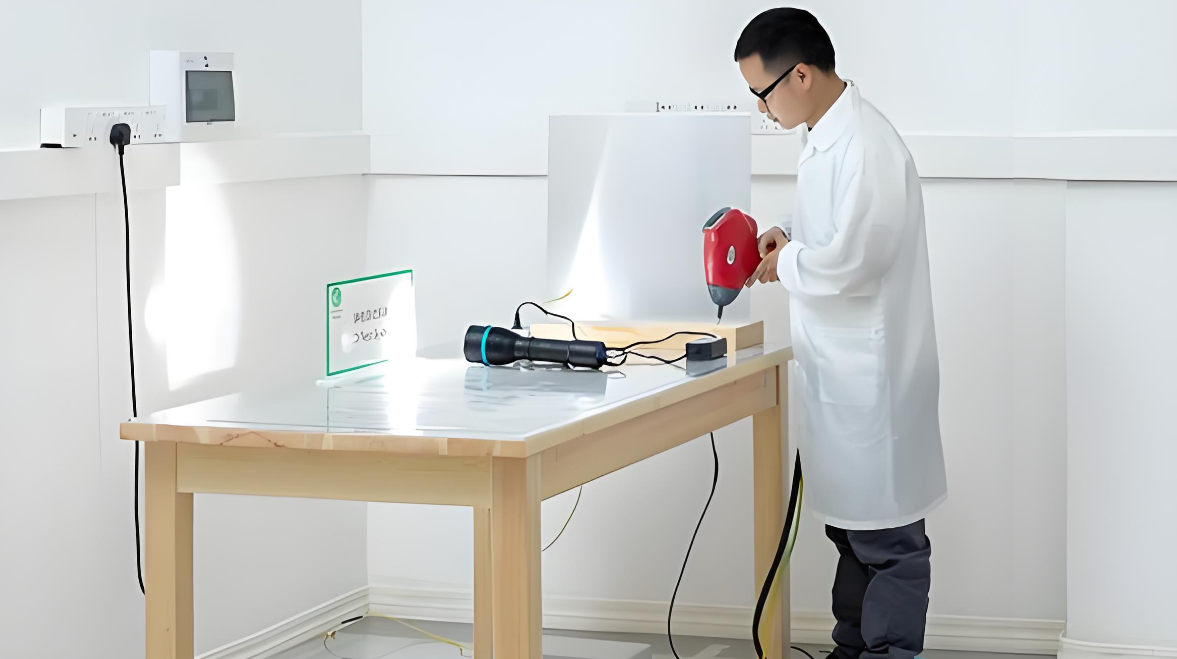
Energie Efficiëntie en Emilieu Standards
ErP-richtlijn (2009/125/EG): Vereist dat LED-producten voldoen aan vereisten voor energie-efficiëntie-etikettering en ecodesign, zoals ERP-certificering. De onderstaande grafiek toont de meest recente Europese energie-efficiëntieklasse die overeenkomt met de lichtefficiëntie:
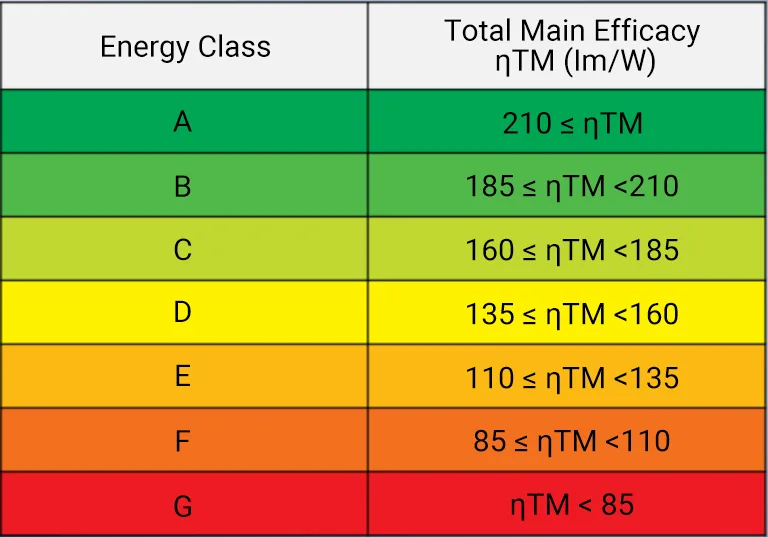
RoHS en REACH: Beperking van het gebruik van gevaarlijke stoffen (bv. lood, kwik) en chemicaliën om ervoor te zorgen dat materialen voldoen aan de milieuvereisten. RoHS (Restriction of Hazardous Substances Directive) is een richtlijn van de Europese Unie (Richtlijn 2011/65/EU), die moet worden omgezet in de nationale wetgeving van de lidstaten om van kracht te worden. REACH is een EU-verordening (Verordening (EG) nr. 1907/2006) en is rechtstreeks van toepassing in alle lidstaten zonder dat omzetting nodig is.
Fotobiologische veiligheid
EN 62471: Evalueert het risico van lichtstraling (bijv. UV, blauw licht) van LED-lichtbronnen om schade aan mensen te voorkomen. Door de intensiteit van de straling, de golflengteverdeling en de blootstellingsduur van de lichtbron te kwantificeren, wordt het risiconiveau geclassificeerd (vrijstellingsniveau, laag, gemiddeld en hoog risico), wordt een veiligheidsbasis geboden voor productontwerp en -gebruik en wordt het risico van chronische oogaandoeningen of huidbeschadiging door lichtstraling verminderd.
Wat are Te Main Tkosten voor LED Neon Sreizen?
Elektrische veiligheidstests
Weerstandstest spanning: Controleer de veiligheid van isolatiematerialen onder hoogspanning. Het belangrijkste doel van de spanningstest is het verifiëren van de isolatieprestaties en de ontwerpmarge van het product om de productkwaliteit te garanderen. Door middel van de weerstandstest kunnen gebreken in het productieproces, zoals onvoldoende kruipafstand of onvoldoende elektrische ruimte, worden opgespoord om de veiligheid van consumenten en de betrouwbaarheid van de producten te beschermen.
Continuïteitstest aarding: Zorgt ervoor dat het aardingssysteem effectief is.
Temperatuurstijgingstest: Evalueert de warmteafvoer van de armatuur bij langdurig gebruik om schade door oververhitting te voorkomen.
Milieu- en mechanische testen
IP-beschermingsniveau testenbijvoorbeeld IP65/IP68 om de water- en stofbestendigheid te evalueren (vooral voor buitentoepassingen).
Zoutneveltest (ASTM B117): Controleert de corrosiebestendigheid.
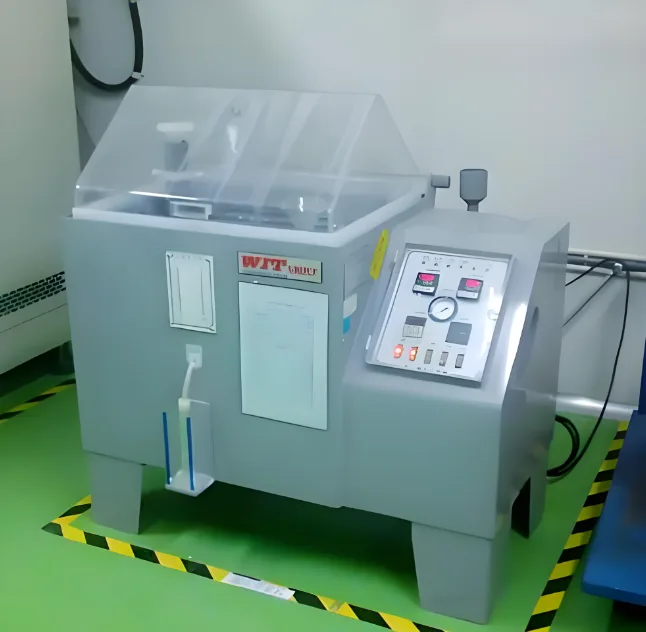
Trillings- en schoktests: Zorg voor structurele stevigheid tijdens transport en gebruik.
Prestatie- en levensduurtests
LM-80: Test het behoud van de lichtstroom en evalueert de levensduur van de LED-chip (er moet worden voldaan aan de normen voor lumenbehoud).
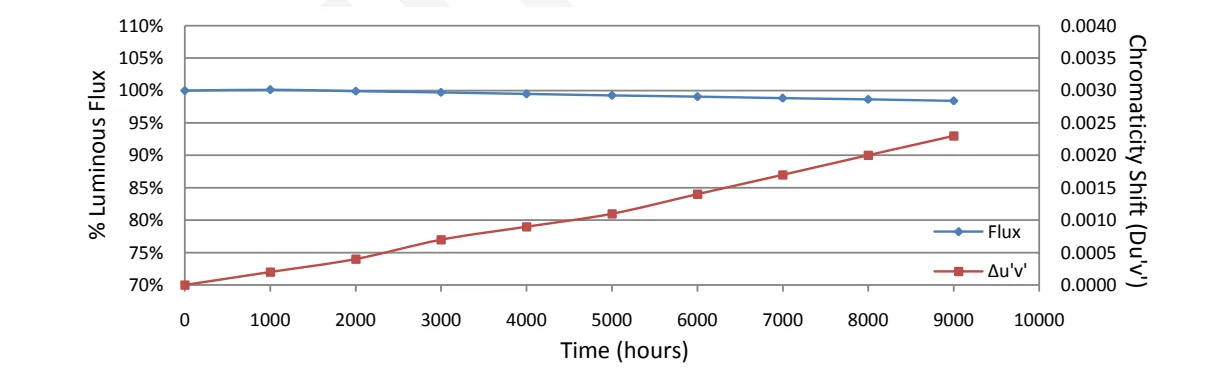
Kleurweergave-index (CRI) test: Meet het kleurweergavevermogen van de lichtbron (aanbevolen I ≥ 80).
LED Neon Sreis Pproductie Pproces Qualiteit Control
1. Materiaal Aankoop: Kies een LED-chip met een hoge kleurweergave-index (CRI ≥ 80) om kleurweergave te garanderen; de buitenmantel moet worden gemaakt van bij voorkeur anti-UV, weerbestendig siliconenmateriaal (beter dan PVC) om vergeling en barsten te voorkomen; de doorschijnende hoes moet zacht en gelijkmatig zijn en een brandklasse van UL94 V-2 of meer hebben. Voeding en draadselectie van UL/CE-gecertificeerde constante stroom- en constante spanningsdrivers; selectie van siliconenlijm voor hulpmaterialen met een temperatuur van -40 ℃ ~ 120 ℃ om langdurige waterdichtheid te garanderen. Vermijd laaggeprijsde accessoires van lage kwaliteit die leiden tot lichtstoringen of veiligheidsrisico's.
2. Uiterlijk Inspectie: Uiterlijk inspectie is een van de belangrijke onderdelen van de LED neon lichtbalk inspectie. Er moet een uitgebreide inspectie van de lichtbalk shell oppervlak vlak is, zijn er geen duidelijke krassen en depressies, de shell kleur uniform is, of de huid is uitgeschakeld, enzovoort. Daarnaast moet je ook controleren of het verbindingsgedeelte van de lichtbalk stevig is, of er een los fenomeen is en of het logo duidelijk en volledig is.
3. Afgewerkt Pproduct Testing: testen van eindproducten, waaronder optische prestatietesten en elektrische prestatietesten.
a) Optisch performance testenDe belangrijkste test is de neonlichtstroom, lichtintensiteitsverdeling, chromaticiteit, lichtefficiëntie en kleuruniformiteit. Inclusief of de lichtkleur nauwkeurig is, de helderheid uniform is, er geen flikkering of kleurverschil is, enzovoort. Tegelijkertijd is het ook nodig om de lichtstroom, het lichtrendement, de kleurtemperatuur en andere parameters van de lichtbalk te meten en te vergelijken om er zeker van te zijn dat deze voldoet aan de relevante normen. Het testen gebeurt meestal met een fotometer of een bolintegratiesysteem. Het meten van de lichtopbrengst met een bol van Ulbricht of fotometer zorgt voor een uniforme helderheid. Controleer of de kleurtemperatuur, kleurweergave-index en kleurtolerantie overeenkomen met de nominale waarde, zoals 3000K warm licht, 6000K koud licht, CRI ≥ 80 en SCDM ≤ 3, om ervoor te zorgen dat de kleur uniform en vrij van afwijkingen is.
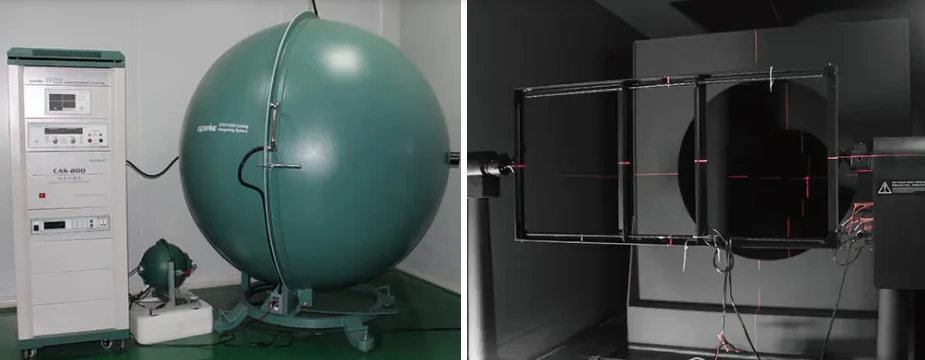
b) Elektrische prestatietest: Inclusief het testen van de stroom van het product, de arbeidsfactor, het vermogen, enz. Meet de spannings- en stroomwaarden van neonstrips onder normale werkomstandigheden om ervoor te zorgen dat de waarden overeenkomen met de nominale parameterbereiken om schade aan de lampen en lantaarns door afwijkingen in de spanning of stroom of veiligheidsrisico's te voorkomen. Door het ingangsvermogen (vermogen = spanning × stroom) te berekenen, kunnen we controleren of het energieverbruik van de neonlichtbalk voldoet aan de ontwerpspecificaties, waarbij we voorkomen dat een te hoog of te laag vermogen de prestaties beïnvloedt.
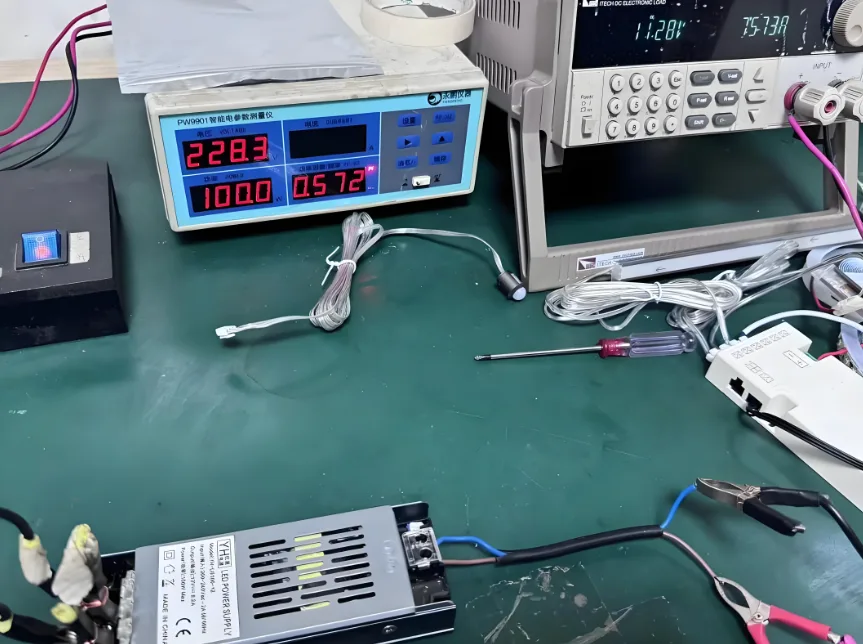
4. Veiligheid PerformatiE Test: De veiligheid prestaties test is om ervoor te zorgen dat de LED neon licht bar niet zal veiligheidsrisico's te produceren in het gebruik van het proces van de sleutel. Moet testen van de veiligheidsprestaties van de strip, met inbegrip van over-temperatuur bescherming en controle circuit abnormale bescherming.
5. Verpakking en Labeling Test: Verpakking en etikettering test om ervoor te zorgen dat de neon strip verpakking intact is, duidelijk gemarkeerd, en nauwkeurige instructies, zakken zijn zonder krassen, er zijn geen kleurafwijkingen, en de grootte voldoet aan de eisen.
6. Duurzaamheidstest: De duurzaamheidstest omvat een lange-termijn gebruik van de LED neon strip test om het werk te simuleren in een verscheidenheid van ruwe omgevingen. De test omvat weerstand tegen hoge temperaturen, weerstand tegen lage temperaturen en waterdichte en stofdichte prestaties om ervoor te zorgen dat de neon strip normaal kan werken in deze omgevingen.
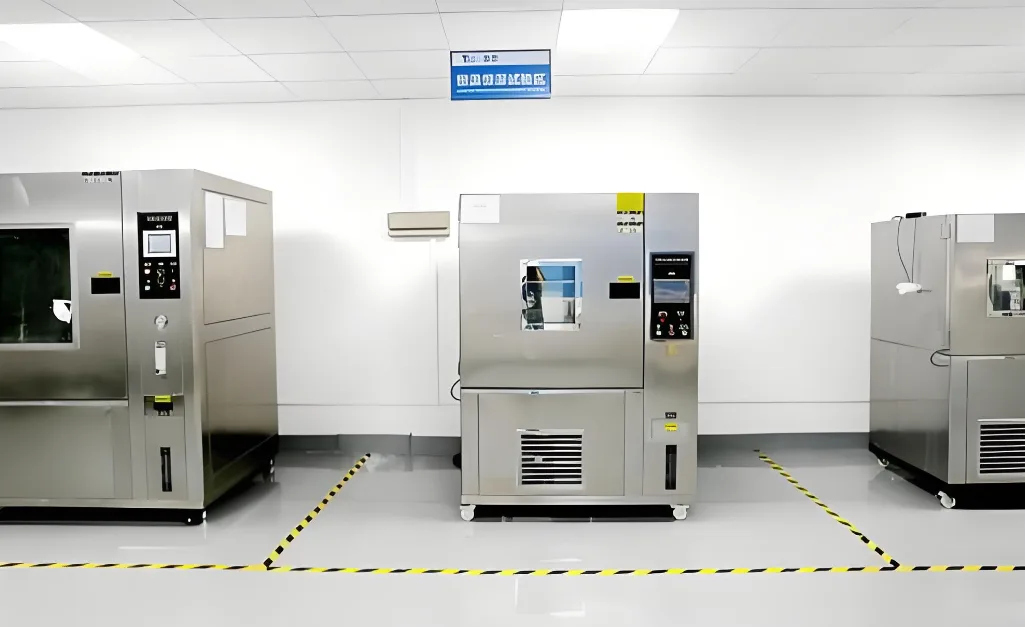
Wat zijn de certificeringsvereisten voor LED Neon Strips?
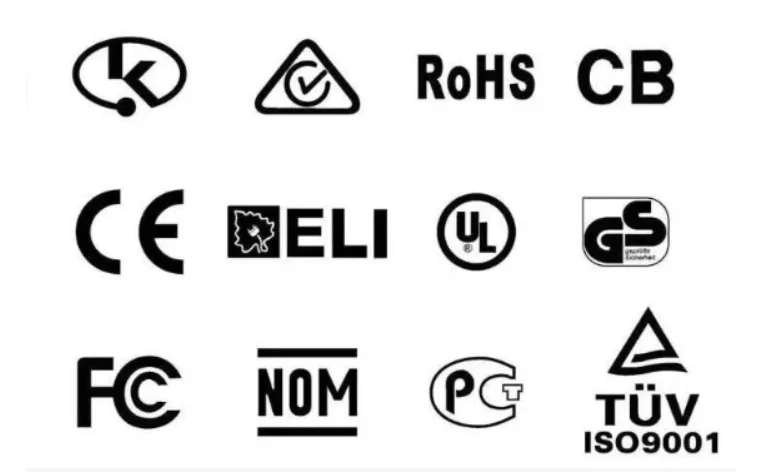
CE Marking: Om op de EU-markt te komen, moet je voldoen aan de CE-markeringstests voor LVD (EN 60598) en EMC (EN 55015/EN 61547).
UL-certificering: Veiligheidscertificering voor markttoegang in Noord-Amerika, met inbegrip van elektrische veiligheid en energie-efficiëntie.
BIS (India) en KC (Korea): Verplichte certificering voor regionale markten, afhankelijk van lokale normen.
LED neon strip certificering zorgt ervoor dat producten voldoen aan bepaalde kwaliteitsnormen op het gebied van ontwerp, materialen, productieprocessen, enzovoort, waardoor ongelukken en geschillen als gevolg van kwaliteitsproblemen met producten worden verminderd en de persoonlijke veiligheid van consumenten wordt gewaarborgd. Gecertificeerde producten hebben meestal een hogere kwaliteit en betrouwbaarheid, wat helpt om het concurrentievermogen van de producten op de markt te verbeteren en het vertrouwen en de tevredenheid van de consument te vergroten.
Veelvoorkomende problemen en risico's
Risico's van Low-kwaliteit Materialen: LED chips of PCB's van slechte kwaliteit kunnen leiden tot snel verval van het licht, kleurafwijkingen of kortsluiting.
Veiligheid Hazards: LED neonlichtbalken met een slechte kwaliteitscontrole kunnen meerdere veiligheidsrisico's met zich meebrengen. Zo kunnen armaturen die niet goed presteren in explosieveilige verbindingen en botsproeven een ontstekingsbron worden in gevaarlijke locaties, waardoor het risico tijdens het gebruik toeneemt.
Prestatieproblemen: LED neon strips van slechte kwaliteit kunnen ook prestatieproblemen hebben. Bijvoorbeeld, sommige producten van de duurzaamheidstest en thermische test, hittebestendigheid, brandwerendheid, weerstand tegen littekens, en andere items niet, wat resulteert in het gebruik van lampen en lantaarns in het proces van gemakkelijke schade of uitval.
Structurele problemen: Structurele problemen zijn ook een veel voorkomend probleem bij slechte kwaliteitscontrole van LED neon strips. Zo kunnen ongekwalificeerde externe bedrading en interne bedrading leiden tot defecte bedrading en kortsluitingsgevaar.
Gevolgen van Lontvangst van Certificering: Als het product niet voldoet aan CE of RoHS kan dit leiden tot een verbod van de EU-markt of hoge boetes.
Conclusie
Kwaliteitscontrole van LED neon strips vereist een combinatie van multidimensionale normen en tests, waaronder certificeringen voor elektrische veiligheid, EMC, energie-efficiëntie en milieubescherming. Fabrikanten moeten de voorkeur geven aan materialen die voldoen aan normen zoals EN 60598 en EN 62471 en die certificeringstests door gezaghebbende organisaties doorstaan (bijv. TÜV, SGS). Daarnaast zijn thermisch beheer en geautomatiseerd testen tijdens het productieproces essentieel om consistentie te garanderen.
SignliteLED is een professionele fabrikant van LED Strip Verlichting En LED Neon Stripverlichting. De fabriek heeft meer complete productie- en testapparatuur, uitgerust met integrerende bollen, EMC-tests, lichtverdelingtesters en andere optische laboratoria; automatische plaatsingsmachines; en test- en verouderingsapparatuur voor hoge en lage temperaturen. De producten voldoen aan de RoHS-normen voor milieubescherming en houden zich aan het hele proces van kwaliteitscontrole, waarbij geautomatiseerde productielijnen worden gebruikt om de betrouwbaarheid van het product te garanderen. SignliteLED heeft veel producten met CE, ETL, UL en andere certificaten; als u ook LED neonlichten wilt kopen, bent u van harte welkom om contact op te nemen met onze zakelijke en technische medewerkers, waar we u zullen helpen een redelijke keuze te maken.