In the fields of commercial display and spatial lighting, edge light boxes have become an important tool for enhancing visual appeal thanks to their unique lighting effects and artistic expressiveness. To design edge light boxes with outstanding effects, it is essential to consider three core elements: optical principles, structural design, and material selection.
An ideal edge light box should achieve uniform light transition and accurate color reproduction while avoiding common issues such as light spot discontinuity or dark edges. Whether it’s creating a soft ambiance for indoor storefronts or meeting the high-brightness requirements of outdoor advertising, a well-designed edge light box can achieve rich, layered, and visually comfortable lighting effects through the clever combination of light and materials.
Light Box Uniformity Testing Method
How should we choose side-lit light boxes? The uniformity of light distribution in light boxes is an important factor to consider. The surface light uniformity of side-lit light boxes directly impacts visual presentation quality and brand communication efficiency.
Even light distribution eliminates bright and dark spots, ensuring accurate color reproduction of text and images and preventing detail loss caused by overly bright or dark areas. This is particularly critical for high-precision printed materials (such as luxury goods advertisements or art exhibition posters). Light uniformity is one of the core indicators for evaluating the professionalism of a lightbox.
Testing method: As shown in the figure below, use a lux meter to take nine measurement points on the lightbox surface (center + four corners + midpoints of the four sides), and calculate the ratio of the minimum value to the average value. During testing, turn off other light sources and maintain a standardized viewing angle of 45°.
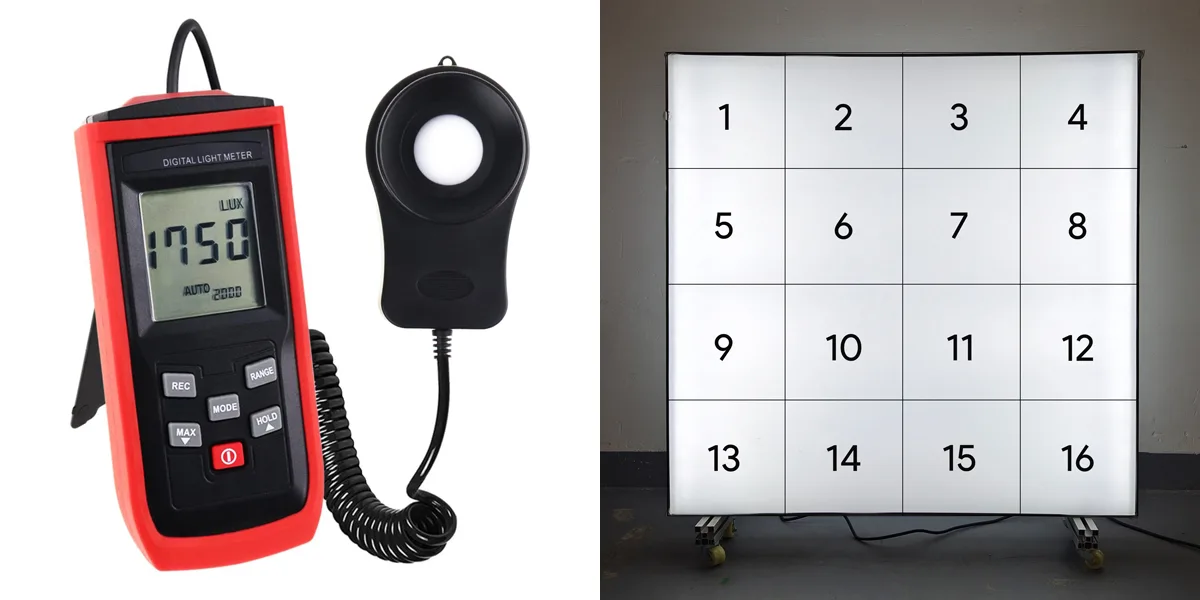
Calculation method: Uniformity = (minimum illuminance value ÷ maximum illuminance value) × 100%. The closer the ratio is to 1 (or percentage ≥ 80%), the more uniform the light distribution.
Insufficient uniformity can cause central bright spots, edge dark areas, or color differences, affecting image clarity and color reproduction, and may even lead to visual fatigue.
Light Box Uniformity Standards
1. Commercial-grade light box standards: Surface brightness uniformity ≥ 80%, minimum brightness value ≥ 80% of average brightness, and average brightness deviation controlled within ±10%.
2. Professional color matching light box standards (e.g., standard light source box): Brightness uniformity ≥ 85%, and must pass the 9-point/25-point method test to ensure that the illuminance difference at any position is ≤ 25%. The color temperature unevenness rate inside the light source box is ≤ 20%.
3. Industrial Inspection Light Box Standards: Such as textile and automotive quality inspection, uniformity ≥ 95%, central area illuminance ≥ 600 lx, edge area uniformity ≥ 85%
4. Side-lit light box standards:
Illuminance uniformity: The ratio of minimum illuminance to average illuminance on the working surface must be ≥0.7 to avoid local dark areas. Side-lit light boxes, due to the light source being located at the edge, may exhibit issues such as a bright center and dark corners. Therefore, there are specific uniformity requirements for light boxes of various lengths:
- Length ≤1 meter: Uniformity ≥85%;
- Length > 3 meters: Uniformity ≥ 70-75%. After illumination, use a luminance meter for on-site testing, with a focus on monitoring the corner positions. If the difference exceeds 20%, it is unqualified;
- Minimum requirements for edge areas: Within 10 cm of the frame: Uniformity ≥ 70% to avoid dark corner phenomena.
LED light bars must have a luminous efficacy > 100 lm/W and use high-transmittance diffusion plates to reduce losses. Measurements are taken at 9 evenly distributed points on the lightbox surface using an illuminance meter, excluding the outer 10% area. There are no national mandatory standards, but compliance with the “Visual Work Requirements” principle in the “Building Lighting Design Standards” (GB50034) is required; In high-reflectivity environments, illuminance may be appropriately reduced; conversely, light source density must be increased.
How should the color temperature of a light box be appropriately configured?
The color temperature matching for side-lit light boxes with LED bars should be determined based on functional requirements and the desired ambiance of the scene. The key lies in the differentiated effects of different color temperatures on visual perception, emotional guidance, and environmental adaptability. To create a pleasant ambiance, it is essential to ensure a reasonable configuration of color temperature and the surrounding environment.
The standard recommended color temperature for light boxes is primarily 6000K–6500K cool white light, which is close to natural daylight (5500–6500K), significantly enhancing visual clarity and color accuracy. This is suitable for high-visibility environments such as shopping malls and exhibition halls and is currently the most widely used primary color temperature for light boxes.
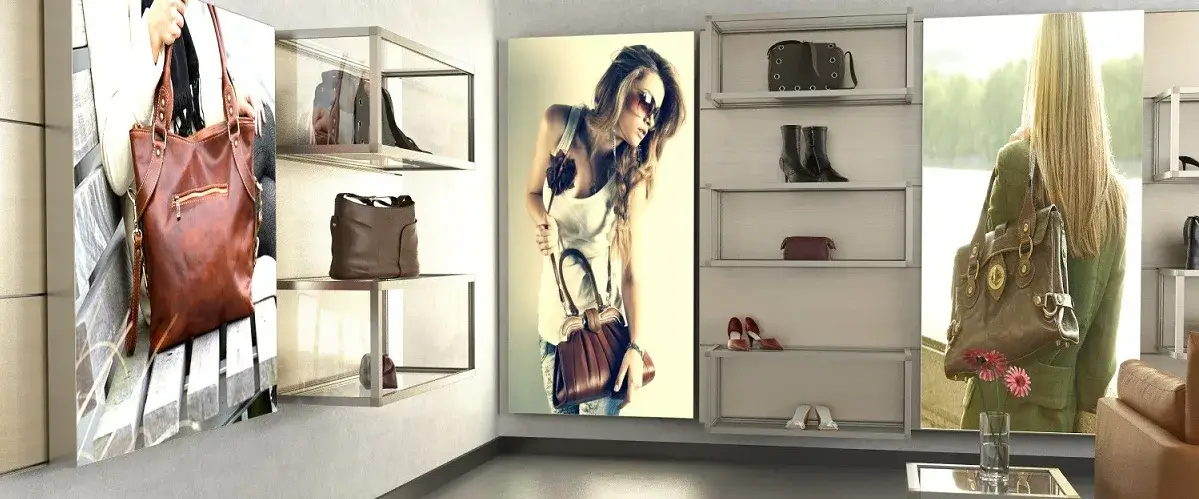
For reading-oriented light boxes or medical display cabinets, where softer lighting is required, neutral light at 4000K–4500K can be selected; for dining establishments (hot pot restaurants/cafés), hotels, and other venues requiring a warm ambiance, a color temperature of 2700K–3500K warm yellow light is recommended to enhance approachability and encourage longer stays.
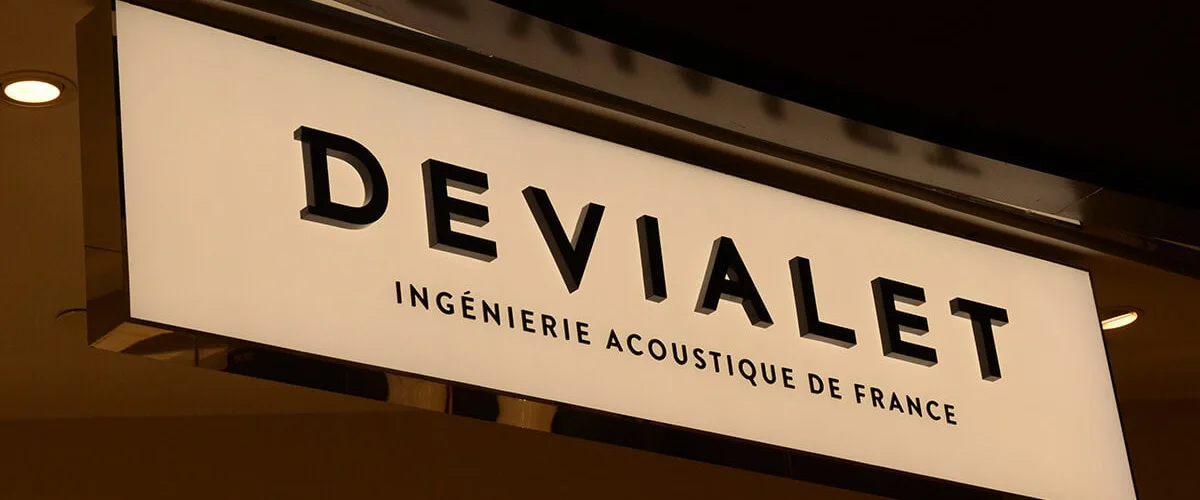
Cool white light with a color temperature >6500K can create a cold, impersonal feel and is only recommended for technology company exhibition halls or long-distance billboards.
Use smart dimmable light strips (adjustable from 3000K to 11000K) to switch between cool white, neutral white, and warm yellow modes via a remote control, adapting to daytime/nighttime or seasonal changes. Example: Art museum light boxes use 5500K during the day to accurately reproduce artwork colors and switch to 3500K at night to create an immersive atmosphere.
Recommended color temperature list for different application scenarios
Application scenario | Recommended color temperature | Visual effect |
Commercial advertising light box | 6000K–6500K | Bright and refreshing, highlighting image details |
Restaurant display cabinet | 2700K–3500K | Warm yellow, cozy, enhances the appeal of food |
Medical/Technology Displays | 4000K–5000K | Neutral and professional, balances seriousness and comfort |
Home Decor Light Boxes | 3000K–4000K | Soft and natural, avoids blue light stimulation |
In summary, the color temperature difference within the same lightbox should be ≤500K to avoid visual fatigue caused by sudden changes in light color. When using multiple lightboxes in combination (such as a store sign array), the color temperature batches must be unified. For more information on color temperature differences, please read the blog 3000K vs 4000K vs 5000K vs 6000K: What’s The Difference?
The color temperature of light boxes should be controlled within ±1000K of the surrounding ambient light temperature. For example, if the main lighting in a store is 4000K, the light box should be selected between 3000K and 5000K. In highly reflective environments such as glass walls, the color temperature should be reduced to below 4500K to minimize glare. Another important metric is the color rendering index (Ra > 80), especially for art displays, to ensure accurate color reproduction. After two years of operation, color temperature drift may exceed 500K, so a 10% brightness reserve should be allocated.
Important notes: Avoid blindly pursuing high color temperatures for a “bright white effect.” Blue light peaks above 6500K may cause visual fatigue and do not comply with the visual health principles of the “Building Lighting Design Standards.”
How to determine the distance and visual effect of side-lit light boxes?
To achieve shadow-free lighting, we must consider the distance between the light box and the choice of light source. As a crucial component of side-lit light boxes, the design characteristics of the light bars directly impact the overall lighting effect of the light box.
As the length of the lightbox increases, the lighting distance of the light source also increases. This requires the lens angle of the edge-lit light strips to be smaller, and a more powerful light source is needed to cover the edge areas, achieving shadow-free lighting. This presents a significant challenge. Let’s explore how to design and configure these elements reasonably to overcome these challenges and achieve the desired lighting effect.
For light sources, we can choose high-power LED chips from reputable brands such as CREE and OSRAM; another important consideration is selecting the appropriate lens. Side-lit lenses must be chosen based on application scenarios, optical performance, technical parameters, and installation compatibility.
Since side-lit light boxes require light projection over longer distances, a beam angle of 10–30 degrees is typically selected. Furthermore, to achieve optimal display performance, on-site testing is required to assess light spot uniformity, edge transitions, and the presence of dark zones. High-quality side-lit lenses must ensure continuous light distribution, avoiding central bright spots or edge attenuation; high luminous flux enhances lighting intensity while balancing glare prevention requirements with a transmittance rate >92%; optical-grade PMMA or PC materials should be prioritized to minimize light attenuation.
To achieve optimal application performance, we conducted multiple tests and selected lenses that met the requirements from a wide range of lens samples. Below are the test data for three different lenses at different distances—PCB length 330mm, using CREE 3535 high-power LEDs. To improve luminous efficiency, a constant-current dimming driver circuit was used, with a power of 14W and luminous efficiency of 120 lm/W. Tests were conducted for both distance and uniformity. The test methods and data are as follows:
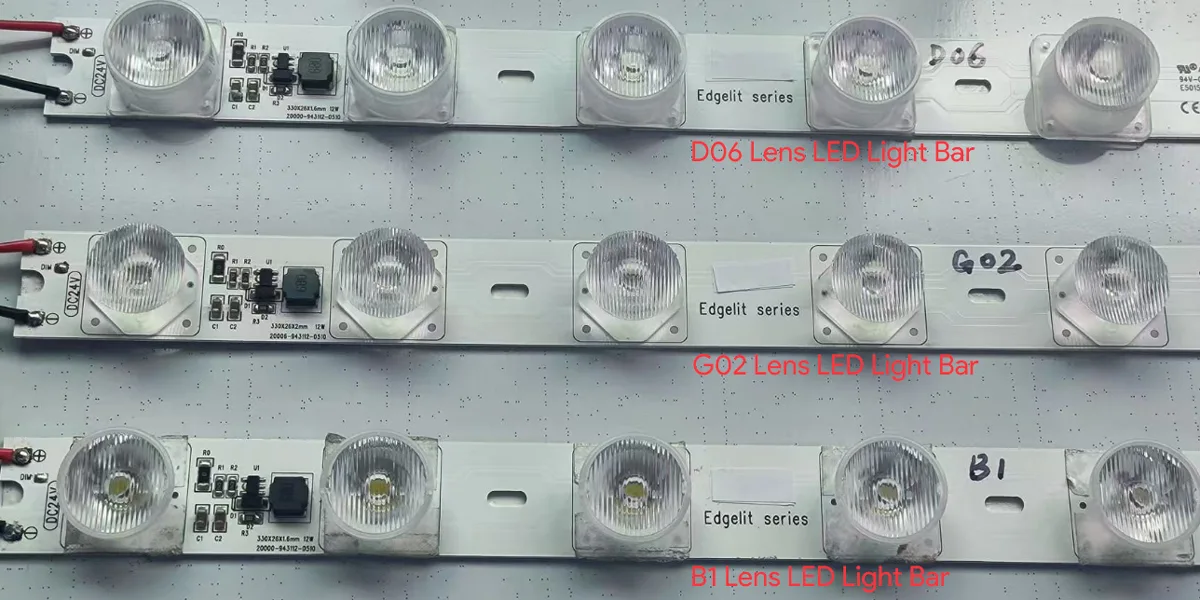
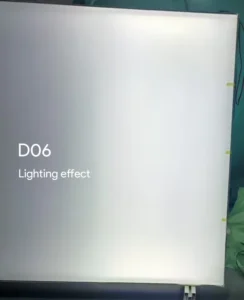
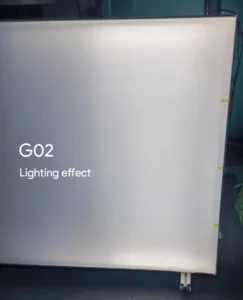
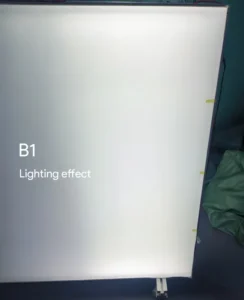
Distance and Illuminance Test List
Item | Lens Type | Beam Angle | 1.0 Meter(lux) | 1.5 Meter(lux) | 2.0 Meter(lux) | 3.0 Meter(lux) |
1 | Lens-G02 | 20×40° | 3650 | 1600 | 860 | 357 |
2 | Lens-B1 | 15×40° | 6070 | 2920 | 1680 | 770 |
3 | Lens-D06 | 15×40° | 3970 | 2250 | 1410 | 690 |
Lens Uniformity Test Data for 1.5×1 Meter Light Box
Lens Type | 150mm(lx) | 300mm(lx) | 450mm(lx) | 600mm(lx) | 750mm(lx) | 600mm(lx) | 450mm(lx) | 300mm(lx) | 150mm(lx) | Average(lx) | Uniformity |
Lens-D06 | 963 | 796 | 768 | 761 | 792 | 810 | 863 | 882 | 996 | 848 | 76.40% |
Lens-G02 | 801 | 676 | 655 | 562 | 558 | 560 | 634 | 658 | 760 | 652 | 69.70% |
From the data, the minimum uniformity value for the D06 lens is 761 lux, and the maximum is 996 lux. 761/996 ≈ 0.74, resulting in a uniformity value of 76.4%, meeting the requirement of over 75%. For the G02 lens, the minimum value is 558 lux, and the maximum is 801 lux. 558/801 ≈ 0.697, resulting in an illuminance uniformity value of 69.7%, which does not meet the standard requirement of 75%. Therefore, the G02 lens is suitable for light boxes under 1 meter in length, while the D06 lens, with a central illuminance exceeding 600 LUX (meeting industrial light box standards), is suitable for light boxes approximately 1.5 meters in length; the B1 lens is suitable for longer distances.
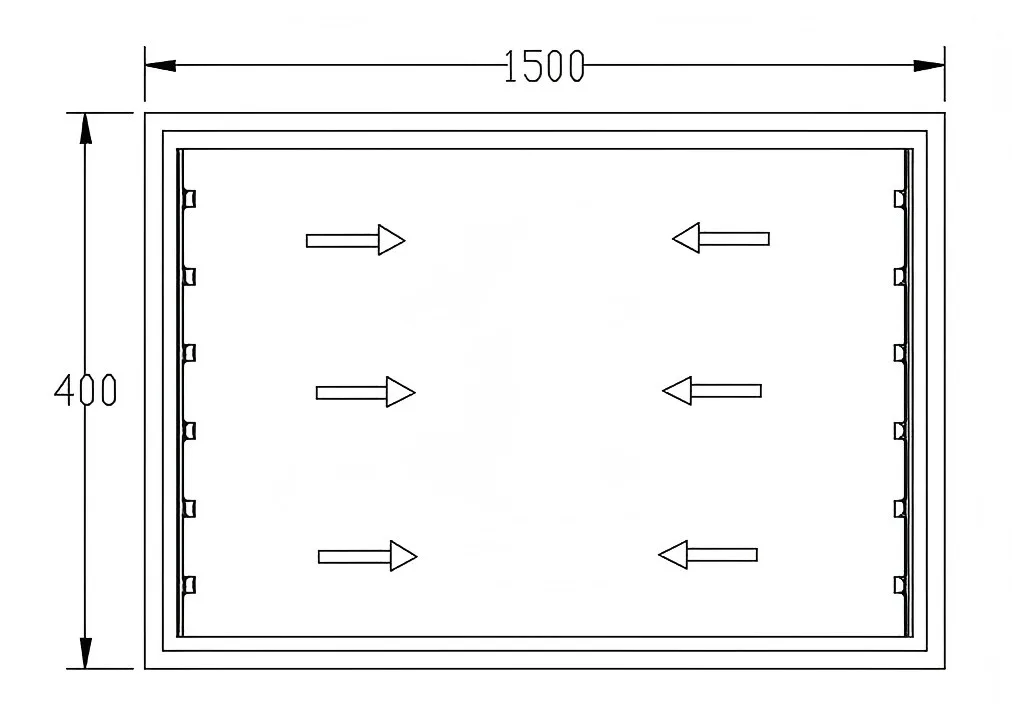
The D06 lens constant current edge-lit light bar is a new product developed by SignliteLED specifically for side lighting. It comes in various installation specifications and lengths to accommodate different light boxes. Under standard specifications, it is suitable for light boxes with lengths of 1 to 2 meters.
More light box and lens tests are currently underway. We will update you as soon as we have new test data and results. Stay tuned!
Lens Uniformity Test for 3×1 Meter Light Box
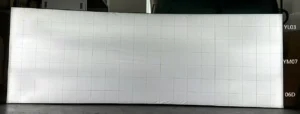
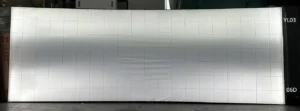
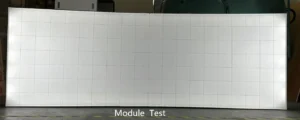
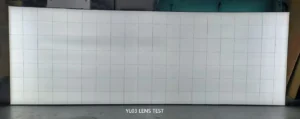
Lens Uniformity Test Data for 3×1 Meter Light Box
Lens Type | Beam Angle | 150mm(lx) | 750mm(lx) | 1500mm(lx) | 750mm(lx) | 150mm(lx) | Average(lx) | Uniformity |
Lens-YL03 | 8×10° | 1098 | 876 | 488 | 749 | 1041 | 850.4 | 57.40% |
Lens-YM07 | 10° | 1459 | 735 | 313 | 740 | 1270 | 903.4 | 34.60% |
Lens-D06 | 15×40° | 1067 | 758 | 282 | 632 | 939 | 735.6 | 38.30% |
Test Conditions: Each lens of 2 pieces 0.3-meter PCB light source, 3 meters apart.
Test Result: Unqualified.
Finished Module Uniformity Test Data for 3×1 Meter Light Box
Lens Type | Beam Angle | 150mm(lx) | 750mm(lx) | 1500mm(lx) | 750mm(lx) | 150mm(lx) | Average(lx) | Uniformity |
MODULE 6.4Wx10pcs | 15×85° | 975 | 302 | 128 | 300 | 874 | 515.8 | 24.80% |
1137 | 359 | 122 | 368 | 1117 | 620.6 | 19.70% | ||
948 | 310 | 128 | 338 | 979 | 540.6 | 23.70% |
Test Conditions: The module was installed on both sides of the light box, with a distance of 3 meters between them.
Test Results: Unqualified.
YL03 Lens Uniformity Test Data for 3×1 Meter Light Box
Lens Type | Beam Angle | 150mm(lx) | 750mm(lx) | 1500mm(lx) | 750mm(lx) | 150mm(lx) | Average(lx) | Uniformity |
YL03 | 8×10° | 1418 | 896 | 780 | 948 | 1350 | 1078.4 | 72.30% |
1530 | 950 | 845 | 993 | 1450 | 1153.6 | 73.20% | ||
1368 | 884 | 754 | 900 | 1387 | 1058.6 | 71.20% |
Test Conditions: The lens light source was installed on both sides of the light box, with a distance of 3 meters between them.
Test Results: Passed.
Introduction to Commonly Used Hard Light Bars for Side-Lit Light Boxes
SignliteLED is a company specializing in the production of side-lit LED light bars, dedicated to providing lighting solutions for light boxes. The company’s specially developed LED rigid light bars for lightbox lighting, featuring unique optical design and engineering advantages, have become the preferred lighting solution for commercial advertising displays. The product employs a diffuse reflection structure to eliminate direct light spots, achieving uniform lighting without dark areas or graininess, with visual effects comparable to natural light.
The product uses high-efficiency LED light sources, reducing power consumption by over 30% compared to traditional light boxes. Combined with an aluminum substrate heat dissipation design, the lifespan reaches up to 50,000 hours, significantly reducing maintenance costs.
Modular side-lit LED light bars support custom lengths, with a maximum single length of 1.5 meters. Installation only requires fixing the frame, and faulty light bars can be replaced independently during maintenance, greatly improving construction efficiency. The lightboxthickness can be reduced to 6 cm while maintaining IP65 waterproof and dustproof performance, making it suitable for outdoor environments. Whether enhancing brand image or optimizing energy efficiency, the light bars perfectly balance functionality and cost-effectiveness.
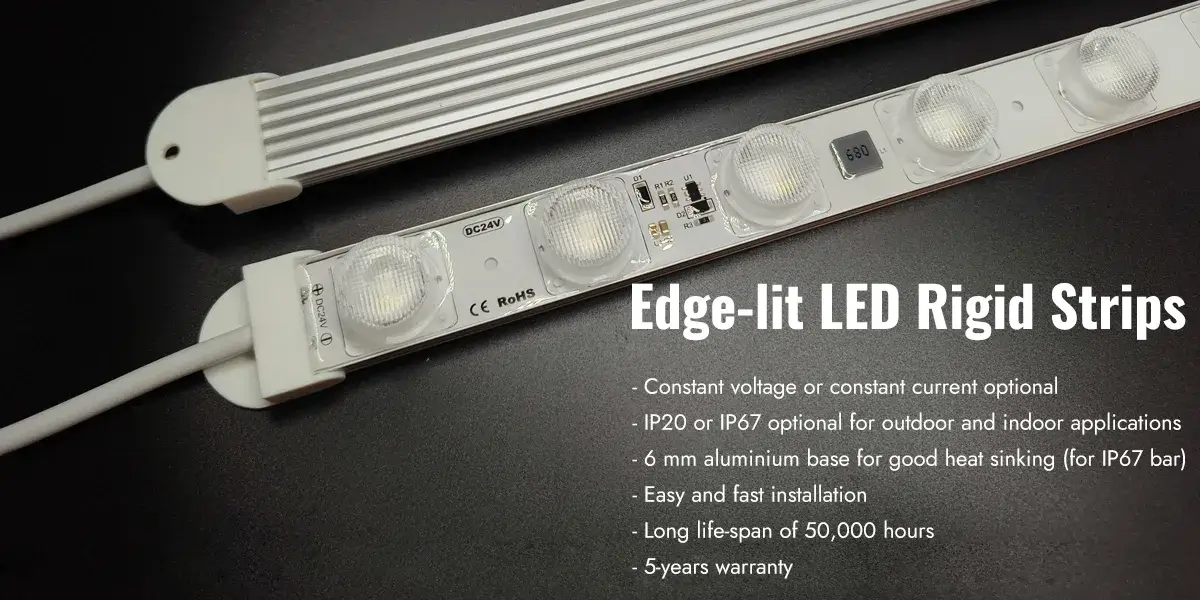
Specifications of Edge-lit Light Box Waterproof LED Rigid Strips
Model NO. | Size(mm) | Beam angle | Input voltage | Power(W) | Eff(lm/W) | Luminous Flux (lm) | Installation depth(cm) | Warranty |
EB265A06W24V | 265X26X15.4 | 15×45° | 24VDC | 6 | 120 | 720 | 6-15 | 5Years |
EB300A06W24V | 300X26X15.4 | 15×45° | 24VDC | 6 | 120 | 720 | 6-15 | 5Years |
EB465A10W24V | 465X26X15.4 | 15×45° | 24VDC | 10 | 120 | 1200 | 6-20 | 5Years |
EB515A10W24V | 515X26X15.4 | 15×45° | 24VDC | 10 | 120 | 1200 | 6-20 | 5Years |
EB633A13W24V | 633X26X15.4 | 15×45° | 24VDC | 13 | 120 | 1560 | 6-25 | 5Years |
EB745A13W24V | 745X26X15.4 | 15×45° | 24VDC | 13 | 120 | 1560 | 6-25 | 5Years |
EB935A20W24V | 935X26X15.4 | 15×45° | 24VDC | 20 | 125 | 2500 | 6-30 | 5Years |
EB965A20W24V | 965X26X15.4 | 15×45° | 24VDC | 20 | 125 | 2500 | 6-30 | 5Years |
EB130A26W24V | 1265X26X15.4 | 15×45° | 24VDC | 26 | 130 | 3380 | 6-30 | 5Years |
EB150A30W24V | 1515X26X15.4 | 15×45° | 24VDC | 30 | 130 | 3900 | 6-30 | 5Years |
The above is a partial list of our products. Custom lengths are available upon request. For more information, please visit our website or contact our technical support team, and we will be happy to assist you.

The Difference Between Constant Current and Constant Voltage LED Rigid Strips
Constant-voltage edge-lit LED strips are typically paired with a 24V low-voltage DC power supply, where the voltage remains stable and constant, while the current automatically adjusts according to the LED chip’s impedance. Each group of lights is equipped with a current-limiting resistor; for example, in a DC24V system, each group typically consists of 6-7 LED chips, with a single current-limiting resistor installed to prevent current overload. This design mitigates the risk of LED damage caused by increased current due to reduced resistance when LED temperatures rise.
Constant-voltage LED bars have a simple structure and low cost, but they rely on resistors for current limiting, which poses a high risk of failure at high temperatures. LED power supplies must provide a stable voltage because LEDs are sensitive to voltage fluctuations. If the voltage is unstable, it may cause uneven brightness in the LED strip and even shorten its lifespan.
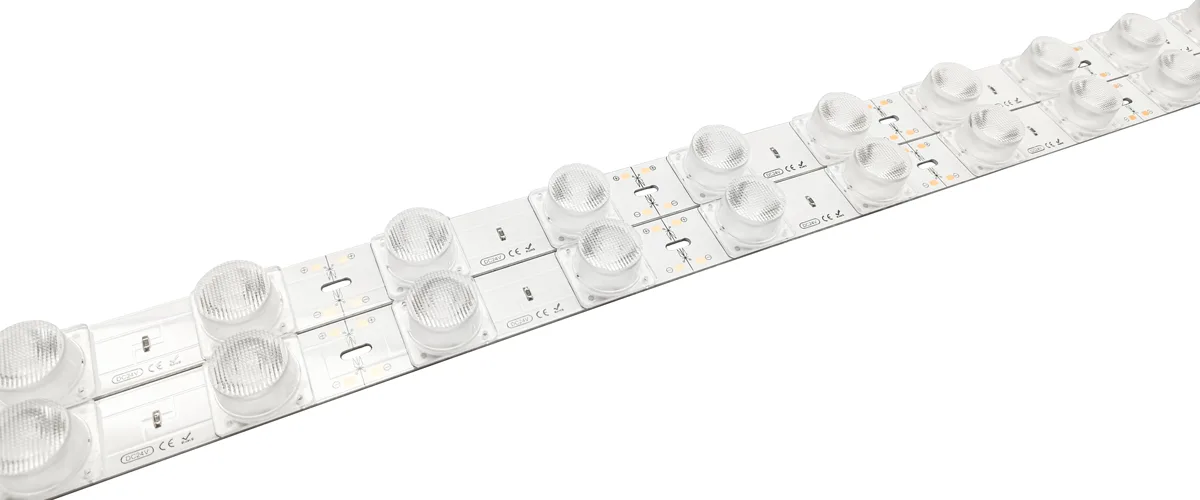
Constant-voltage LED rigid strips have the following characteristics:
● Standardized voltage: Common DC24V constant-voltage power supplies are highly compatible with LED strip specifications, allowing users to directly purchase power supplies of the corresponding voltage without complex calculations.
● Universal installation: Constant-voltage power supplies directly match the rated voltage of the lighting fixtures, enabling operation upon connection. They support length customization and offer flexible installation options.
● Adaptive intelligence: Constant-voltage LED bars can be paired with PWM dimmers or smart controllers to adjust brightness and color, meeting the needs of smart light boxes and home lighting applications.
Constant-current side-lit LED rigid strips are typically also powered by DC 24V, providing a constant current output with voltage dynamically adjusted based on the number of LED chips. The LED board integrates a constant-current driver chip, which precisely controls the output current via a current-sensing resistor, ensuring stable operating current for each LED chip. Even with minor input voltage fluctuations of ±10%, the LED current remains constant, resulting in more stable brightness and extended LED lifespan.
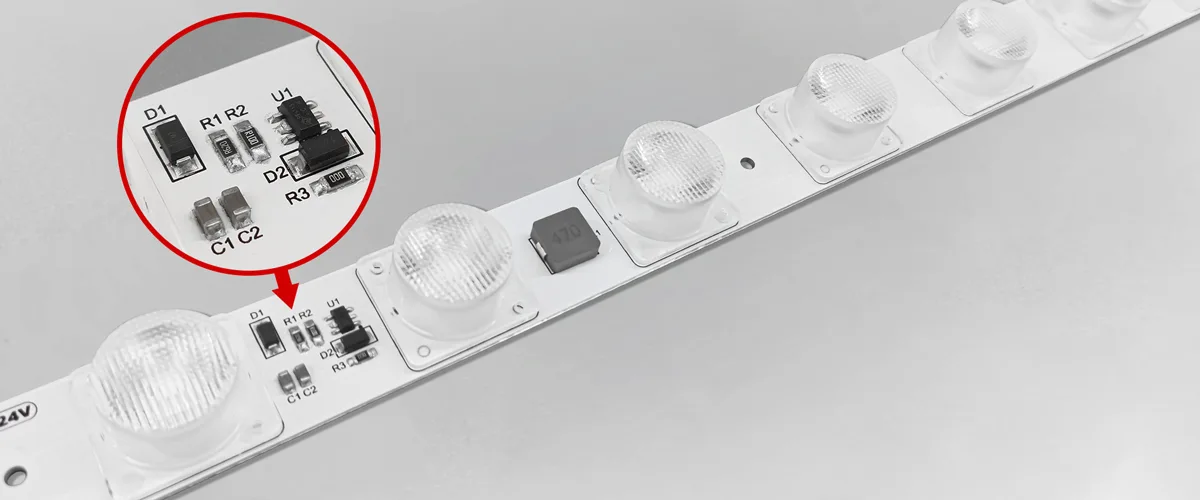
Constant-current LED rigid strips have the following features:
● Voltage fluctuation resistance: The constant-current driver automatically adjusts the output current, maintaining a constant current even with ±10% input voltage fluctuations, preventing brightness unevenness or flickering caused by sudden current changes in the LEDs. In contrast, with a constant-voltage driver, a 10% voltage fluctuation may cause a 30% current fluctuation, directly affecting brightness and lifespan.
● Temperature adaptability: The chip incorporates negative temperature compensation functionality, automatically reducing current when temperature rises to prevent LED overheating and light decay, with an operating temperature range of -40°C to 125°C.
● Overload and short-circuit protection: The constant-current drive chip integrates over-temperature protection and over-voltage protection. Under abnormal conditions, it automatically limits current or shuts down to prevent LED burnout. In a series circuit, even if a single LED shorts out, the remaining LEDs can continue to function normally.
● Minimal light decay: By precisely controlling the current, it reduces heat accumulation in LEDs during long-term operation, slowing down light decay. This further minimizes the impact of system temperature rise on the LEDs.
Constant Current vs. Constant Voltage LED Rigid Strip
Performance ComparisonCharacteristics | Constant Voltage LED Rigid Strip | Constant Current LED Rigid Strip |
Brightness Stability | Significant voltage drop over long distances, inconsistent brightness at both ends | No voltage drop, consistent brightness over long distances |
Lifespan Performance | Resistor failure can cause light decay, lifespan approximately 20,000 hours | Negative temperature compensation design, lifespan up to 50,000 hours |
Failure Impact | Single LED failure does not affect other LEDs | Single LED failure causes the entire strip to go out |
Energy Efficiency | Conversion efficiency approximately 80-85%, significant resistor heat loss | Constant current efficiency >90% |
Cost | Simple structure, low cost | Complex structure, cost approximately 10%-15% higher than constant voltage |
Should edge-lit LED rigid strips use constant current or constant voltage?
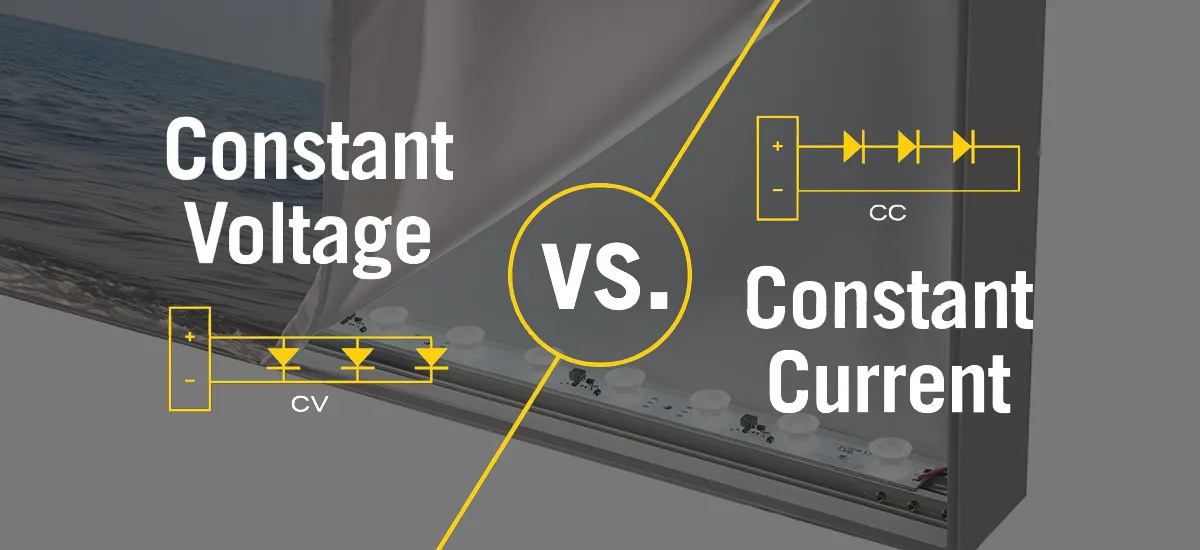
Constant current rigid strips offer significant technical advantages over traditional constant voltage drive solutions, primarily in terms of brightness stability, extended lifespan, and high energy efficiency. Constant current rigid strips typically use PWM dimming, while constant voltage rigid strips offer strong dimming compatibility, supporting PWM, 0-10V, and triac dimming.
Constant-voltage LED rigid strips are suitable for small light boxes with distances less than 1 meter, as voltage drop over short distances can be ignored, and they are more cost-effective, making them ideal for decorative light boxes with limited budgets. Constant-current drives have no voltage drop issues, ensuring uniformity in long-distance side lighting and avoiding dark areas at the edges of light boxes, making them suitable for large light boxes with distances over 2 meters.
Side-lit LED rigid strips are typically fixed installations prioritizing long-term stability. Constant current solutions offer significant advantages in brightness consistency and lifespan. For low-cost flexible retrofits, constant voltage drivers can be selected, but circuit protection must be reinforced. The final choice should be balanced based on budget, installation complexity, and lighting performance requirements.
Summary
SignliteLED has specialized in the production of LED strip lights and LED sign tubes for many years. Our LED sign tubes and custom LED light bars for light boxes come in a wide variety of types, compatible with various specifications of light boxes. Whether you’re upgrading an existing signage system or developing a new installation, SignliteLED can provide a reliable, high-performance LED light box lighting solution tailored to your exact requirements.